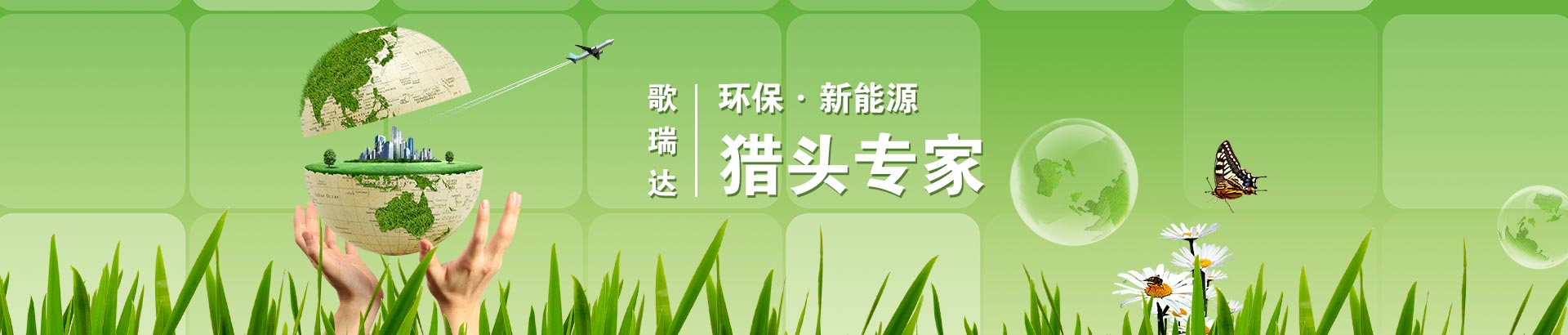
動(dòng)力電池產(chǎn)能過(guò)剩導(dǎo)致儲(chǔ)能梯次利用難
時(shí)間:2018-09-11 來(lái)源:admin
儲(chǔ)能電池比動(dòng)力電池要求高得多,現(xiàn)在1500—2000個(gè)循環(huán)就足以滿足乘用車對(duì)動(dòng)力電池的要求,但儲(chǔ)能電池的要求是至少8000個(gè)循環(huán)。一直以來(lái),行業(yè)有一種誤解,認(rèn)為過(guò)剩產(chǎn)能所留下來(lái)的庫(kù)存動(dòng)力電池都能被用到儲(chǔ)能上。
據(jù)研究統(tǒng)計(jì),2018年前7月共計(jì)生產(chǎn)45.5萬(wàn)輛,同比增長(zhǎng)84.2%;實(shí)現(xiàn)裝機(jī)18.8GWh,同比增長(zhǎng)137%,動(dòng)力電池前十企業(yè)占據(jù)市場(chǎng)份額已達(dá)90%以上。其中,CATL的占比不斷提高。SPIR預(yù)計(jì),未來(lái)二到三年,市場(chǎng)集中度將由集中走向分散,然后再走向集中化。行業(yè)預(yù)計(jì),2020年新能源汽車的產(chǎn)能將達(dá)到210萬(wàn)輛,對(duì)應(yīng)的動(dòng)力電池裝機(jī)量將為101GWh。2017年中國(guó)動(dòng)力電池的產(chǎn)能就已經(jīng)超過(guò)了200GWh,但是產(chǎn)能利用率卻只有40%。
2018年上半年還有一個(gè)很有意思的現(xiàn)象,無(wú)論是電池材料還是電池本身出貨均顯著弱于終端增長(zhǎng),上游原材料及輔料出現(xiàn)快速降價(jià)的情況。比如一向生猛的“鈷奶奶”9月的報(bào)價(jià)已跌至47萬(wàn)元/噸,4月初便開(kāi)始便由漲轉(zhuǎn)跌,至今跌幅已超過(guò)25%,市場(chǎng)情緒隨之轉(zhuǎn)弱。相關(guān)部門(mén)認(rèn)為鈷價(jià)不斷下跌的主要原因是2017年下半年以來(lái),全產(chǎn)業(yè)鏈備庫(kù)存力度較大,導(dǎo)致中游總體處于去庫(kù)存的狀態(tài)。隨著下半年車企普遍進(jìn)入銷售旺季,長(zhǎng)達(dá)半年多的持續(xù)去庫(kù)存之后,目前電池廠的庫(kù)存狀態(tài)應(yīng)該在合理區(qū)間。此外,2018年新執(zhí)行的補(bǔ)貼方案將最低續(xù)航里程要求由2017年的100公里調(diào)整到150公里,電池系統(tǒng)的最低能量密度要求由2017年的90Wh/kg調(diào)整為105Wh/kg。車企提前停止生產(chǎn)低續(xù)航里程的車輛,導(dǎo)致一批電池“被下崗”。
很多人說(shuō)過(guò)剩產(chǎn)能是可以用到儲(chǔ)能上去的,實(shí)際這里有很大的誤解,儲(chǔ)能電池比動(dòng)力電池要求高得多,現(xiàn)在1500—2000個(gè)循環(huán)就足以滿足乘用車對(duì)動(dòng)力電池的要求,但儲(chǔ)能電池的要求是至少8000個(gè)循環(huán)。落后的產(chǎn)能可能會(huì)逐漸被淘汰。影響電池梯次利用的一大障礙是電池規(guī)格的不匹配,現(xiàn)在電池的型號(hào)不一,配組時(shí)需要的電池量基數(shù)將很大,篩選、配組和加工的成本仍相對(duì)較高,只有少數(shù)技術(shù)成熟的企業(yè)才能獲取經(jīng)濟(jì)效益。
不能用于儲(chǔ)能和低端電器的電池最終只能通過(guò)回收,拆解其中的貴金屬進(jìn)行梯次利用。目前磷酸鐵鋰的拆解效益很小,最有價(jià)值的市場(chǎng)在三元鋰電池方面。電池回收現(xiàn)在還存在成本方面的問(wèn)題,比如碳酸鋰的價(jià)格只有在10萬(wàn)/噸以上回收才能保本,不過(guò)相信隨著回收技術(shù)的進(jìn)步,回收的價(jià)值會(huì)越來(lái)越大。